Кризис больно ударил по промышленным предприятиям республики. ОАО "Алагирский завод сопротивлений", одно из ведущих в системе резисторостроения в России, и вовсе могло прекратить работу из-за отсутствия объемов производства, прошлый год стал критическим для предприятия с полувековой историей. Сохранили заводу жизнь практичный подход к делу и энергия его руководства и коллектива.
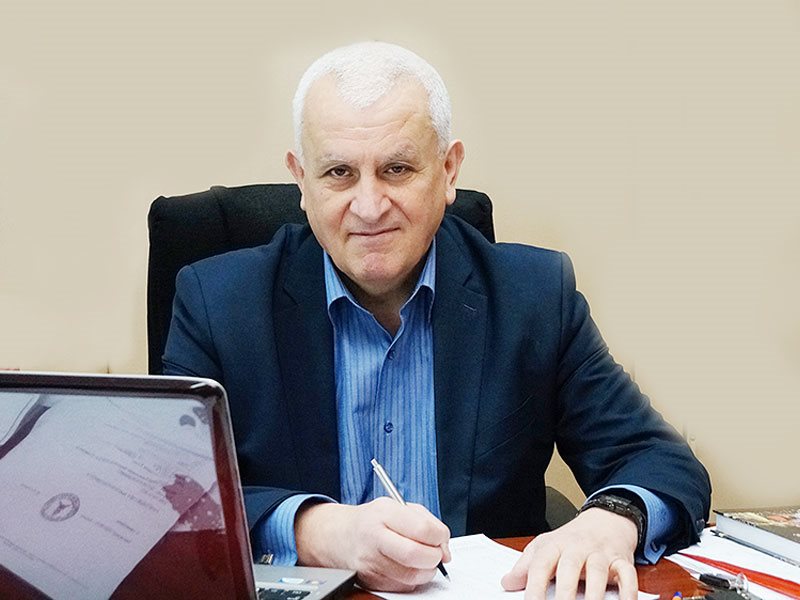
Трудовая активность на АЗС в последние месяцы связана с производством нового типа изделий – влагостойких резисторов, которые используются в электроцепях переменного и постоянного тока, для эксплуатации в условиях высокой влажности или температур. Заказчики – фирмы, предоставляющие услуги для ОАО "РЖД", предприятия оборонного комплекса и другие.
Как происходит выпуск освоенной продукции? Корреспонденты "СО" увидели это своими глазами.
Все этапы производства резисторов сосредоточены в одном корпусе. В цехе № 1, куда нас первым делом провел замгендиректора по экономике и производству Алан Каргинов, идут армировка, окраска, маркировка, окончательная приемка и упаковка изделий. И хотя мы не увидели высокотехнологичного конвейера, за эти полгода АЗС сумел освоить новое изделие, провести испытание и выйти на рынок. Сегодня работа в цехе идет полным ходом, несмотря на сложные условия. Только этих изделий за столь короткие сроки предприятием произведено на сумму около 2 млн руб.
"С началом изготовления на заводе более усовершенствованного резистора есть надежда сделать прорыв и занять до 30% рынка против нынешних 10%. В планах предприятия увеличить вдвое объемы производства, – делится Алан Каргинов. – Считаю, первый удачный шаг завод сделал. Теперь осталось доказать, что мы можем конкурировать и по качеству, и по срокам изготовления, а также используя гибкую ценовую политику".
В технологической цепочке изготовления резисторов задействованы около 20 человек. Один из ответственных процессов – покраска.
Окрашенные вручную изделия рабочие сушат в специальных установках при высоком температурном режиме. Именно так происходит полимеризация компонентов грунтовки и краски.
"К нам изделие попадает после намотки и сварки. Наша задача – избежать неравномерного покрытия в процессе, когда высокая температура расплавляет песок, который обволакивает и покрывает весь резистор. Других сложностей в нашей работе нет", – говорят окрасчики резисторов Зарина Кусраева и Белла Льянова. За процессом производства строго следят работники отдела контроля качества.
"Электрические параметры – это самое основное в технических характеристиках изделия. Только потом смотрю маркировку и оцениваю внешний вид, чтобы не было сколов и оголений. Мелкие дефекты встречаются изредка, исправить их не составляет труда", – рассказывает инженер контроля качества Белла Агнаева.
"Это последняя инстанция, которая дает добро, перед тем как мы отправим продукцию потребителю. Без метки ОТК ни одно изделие не выйдет с завода. Этим мы гарантируем качество резисторов", – дополняет Алан Каргинов.
У предприятия есть постоянные заказчики, которые не меняются многие годы – это предприятия оборонно-промышленного комплекса, мы поставляем им 65-70% производимой продукции, Завод рассчитывает улучшить свое финансово-экономическое положение, а также увеличить номенклатуру производимой продукции и ее объемы
А чтобы не было сбоев в самом процессе, важно вовремя получить комплектующие материалы. За этот вопрос в цехе отвечает "легенда завода", как ее здесь с уважением называют, мастер участка № 1 Тамара Дзбоева. Она пришла на завод еще совсем юной – в далеком 1965 году. "Рабочий день цеха начинается с нее и заканчивается ею, – говорит замдиректора. – Утром Тамара раздает необходимый материал, а вечером у нее другая задача – обеспечить отгрузку. Имея многолетний стаж и опыт, она так легко и быстро делает свою работу, что, кажется, заменяет несколько человек".
Не последнюю роль во всем этом процессе играет организация рабочего места. По словам Алана Каргинова, завод своими силами переоборудовал сборочные столы и приспособления, настроив их на мелкосерийное производство. "Сложность была в том, чтобы унифицировать это изделие с нашим основным, которое мы изготовляем", – говорит замдиректора. Задача была успешно решена.
По мере сил и возможностей решается также вопрос кадров. Со слов начальника отдела кадров Мурата Купеева, относительно недавно на завод принял двух новых сотрудников, но этого мало, учитывая, что средний возраст рабочих – около 60 лет. Причина такого положения дел, по его мнению – в низкой заработной плате. Однако молодые специалисты на завод все же приходят. В их числе – Чермен Урумов, наставниками которого являются ветераны – мастер Еза Губаева и наладчик технологического оборудования Алан Гутиев. В настоящее время он отвечает за участок № 4, где происходит штамповка металлических деталей.
"Всего четыре месяца, как Чермен возглавил участок. Нас покорили его прилежность и талант – он освоил такие станки, на которые мы не могли найти специалистов здесь, в республике, планировали привлечь их со стороны. А это могло дорого нам обойтись", – продолжает нас знакомить с тружениками завода замдиректора.
Нам показали накатные станки, на которых делают винты разных диаметров. Молодой специалист Чермен Урумов – выпускник Балтийского государственного технического университета "Военмех" – не просто освоил станок, но и починил его.
"Снята большая проблема, то есть, если сейчас деталь нам обходится в рубль, то при заказе на стороне пришлось бы заплатить 10–12 рублей", – поясняют заводчане.
"У предприятия есть постоянные заказчики, которые не меняются многие годы – это предприятия оборонно-промышленного комплекса, мы поставляем им 65-70% производимой продукции, – рассказывает генеральный директор ОАО "АЗС" Анатолий Сопоев. – Завод рассчитывает улучшить свое финансово-экономическое положение, а также увеличить номенклатуру производимой продукции и ее объемы, тем более что глава республики озвучил курс на поддержку промышленных предприятий".
За последние 20 лет сокращений на заводе не допустили. Средняя зарплата – 10 тыс. руб., задолженности по ней нет, всего трудоустроены 165 человек. Теперь с освоением нового типа резисторов задача – крепко встать на ноги.
"Мы выпускаем узкопрофильную продукцию. Она расходится по всей России, это 80 предприятий. В 2017 году произведено продукции на 26 млн руб., что на 3% больше, чем в позапрошлом. В динамике ежегодно прибавляем до 2–3%. Но эти объемы нам многого стоят", – признается Анатолий Сопоев. Но желание двигаться вперед, судя по всему, у коллектива АЗС и его директора только укрепляется.
-
Зажженный вами не погаснет свет!05.10.2018 14:45Редакция01.01.2017 8:00
-
Реклама и реквизиты01.01.2017 2:30Упрощенная бухгалтерская (финансовая) отчетность01.05.2016 17:45
-
Разжижаем кровь13.06.2018 16:45Фокус фикуса Бенджамина27.09.2024 15:25
-
ОрджВОКУ - 100 лет!20.11.2018 12:15150-летие технологическому колледж полиграфии и дизайна, 15 октября 201830.10.2018 15:30